新書推薦:
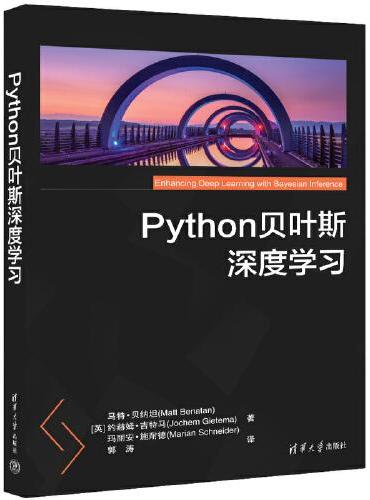
《
Python贝叶斯深度学习
》
售價:HK$
89.4
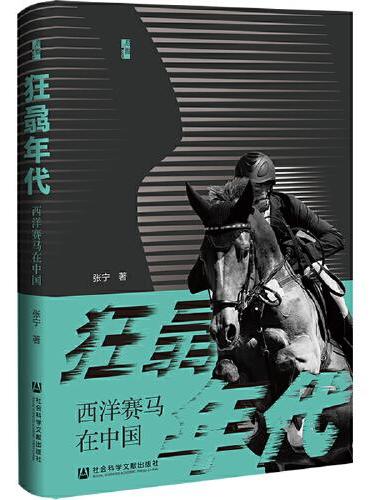
《
启微·狂骉年代:西洋赛马在中国
》
售價:HK$
78.4
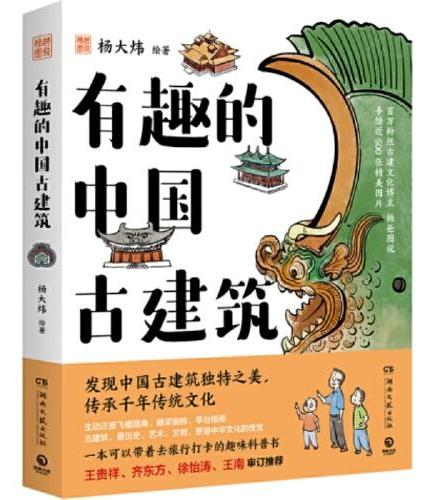
《
有趣的中国古建筑
》
售價:HK$
67.0
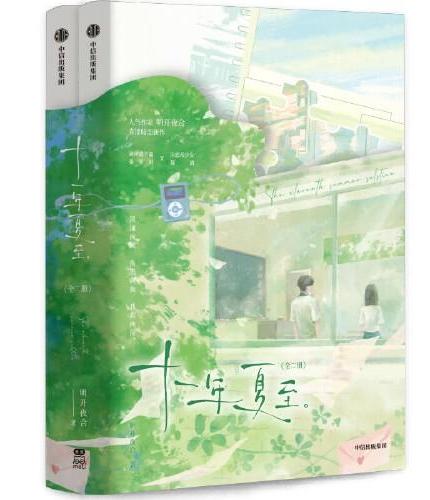
《
十一年夏至
》
售價:HK$
76.2
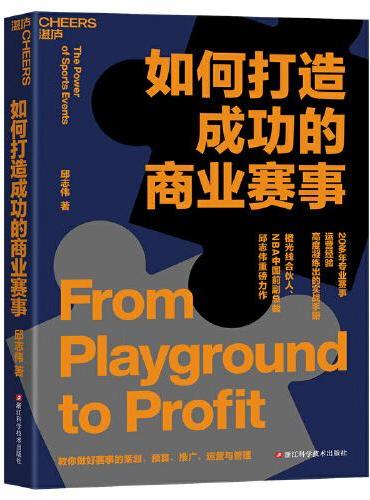
《
如何打造成功的商业赛事
》
售價:HK$
89.5
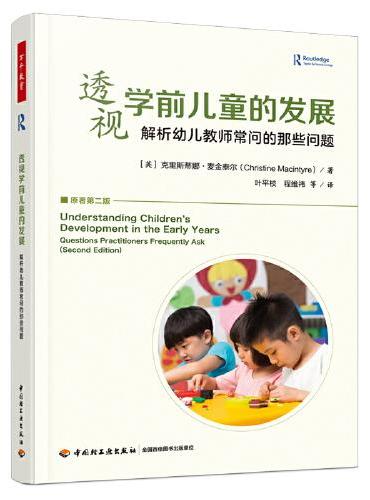
《
万千教育学前·透视学前儿童的发展:解析幼儿教师常问的那些问题
》
售價:HK$
58.2
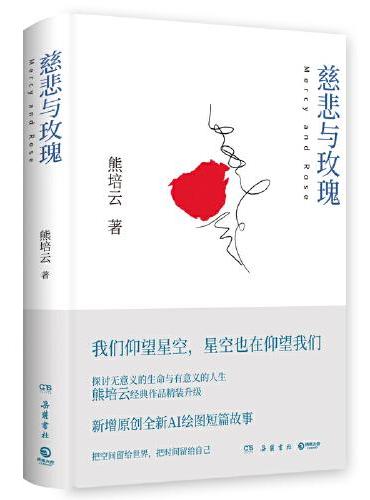
《
慈悲与玫瑰
》
售價:HK$
87.4
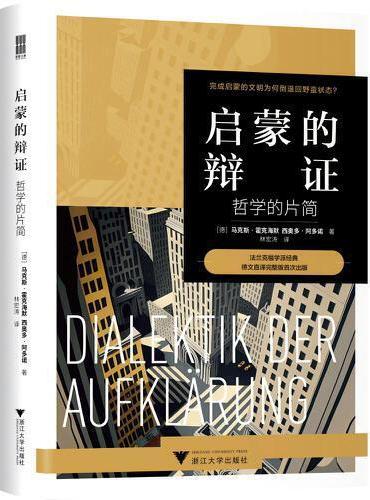
《
启蒙的辩证:哲学的片简(法兰克福学派哲学经典,批判理论重要文本)
》
售價:HK$
76.2
|
編輯推薦: |
丛书特色:设计师职业培训教程丛书拥有完善的知识体系和教学套路,按照教学天数和课时进行安排,采用阶梯式学习方法,对设计专业知识、软件的构架、应用方向以及命令操作都进行了详尽的讲解,循序渐进地提高读者的应用能力。
编辑推荐:本书将设计项目时的思路、流程、方法和技巧、操作步骤面对面地与读者交流,是广大读者快速掌握应用软件的自学实用指导书。图书还配备了交互式多媒体教学演示光盘,将案例制作过程制作为多媒体视频进行讲解,有从教多年的专业讲师全程多媒体语音视频跟踪教学,便于读者学习使用。本书还提供了网络的免费技术支持,欢迎大家登录云杰漫步多媒体科技的网上技术论坛进行交流。论坛分为多个专业的设计板块,可以为读者提供实时的软件技术支持,解答读者问题。
|
內容簡介: |
UG NX是当前三维CADCAM软件中使用最为广泛的应用软件之一,广泛应用于通用模具设计和数控加工各行业中,其最新版本是UG NX 10中文版。本书从实用的角度介绍了UG NX 10中文版软件的模具设计和数控加工功能。全书分6个教学日,共45个教学课时,主要包括模具设计入门、初始化设置、腔体设计、分型线设计、分型面设计、型芯与型腔设计、模架设计、数控加工基本操作、面铣削加工、型腔铣削加工、轮廓铣加工、点位加工和数控车削加工等内容。另外,本书还配备了交互式多媒体教学光盘,便于读者学习使用。
本书结构严谨、内容翔实,知识全面,写法创新实用,可读性强,设计实例专业性强,步骤明确,主要面向使用UG NX进行模具设计和数控加工的广大初、中级用户,可以作为大专院校计算机辅助设计课程的指导教材和公司模具设计培训的内部教材。
|
關於作者: |
作者长期从事CAD的专业设计和教学工作,数年来承接了大量的项目,具有丰富的实践经验。
|
目錄:
|
目 录
第1教学日1
第1课 设计师职业知识模具塑料及成型
工艺2
1.1.1 模具成型工艺2
1.1.2 模具的结构和类别4
第2课 模具设计基础知识7
1.2.1 模具设计的基本流程7
1.2.2 模具型腔的设计7
第3课 UG NX 10.0模具模块11
1.3.1 NX模具设计术语12
1.3.2 注塑模设计界面介绍13
1.3.3 NX塑料注塑模具的设计流程15
课后练习16
第4课 NX 10.0注塑模向导及入门25
1.4.1 初始化项目25
1.4.2 产品分型31
1.4.3 模架库及标准件36
课后练习39
阶段进阶练习46
第2教学日47
第1课 设计师职业知识冲压模具及原理48
第2课 模型初始化51
2.2.1 装载产品模型51
2.2.2 模具坐标系和收缩率55
2.2.3 工件设计58
课后练习60
第3课 多腔模模具型腔68
2.3.1 多腔模布局68
2.3.2 多件模设计73
2.3.3 重定位方法74
2.3.4 插入腔和删除布局76
课后练习77
第4课 注塑模修补工具80
2.4.1 创建方块80
2.4.2 分割工具82
2.4.3 修补破孔83
2.4.4 其他工具87
课后练习91
阶段进阶练习94
第3教学日95
第1课 设计师职业知识模具分型概述96
第2课 创建区域和分型线98
3.2.1 分型概述98
3.2.2 创建分型线100
3.2.3 编辑分型线和引导线102
课后练习104
第3课 分型面的创建与操作113
3.3.1 分型面创建113
3.3.2 分型面操作116
课后练习117
第4课 创建型芯和型腔125
3.4.1 设计和提取区域125
3.4.2 模具分型127
3.4.3 模型比较与分析129
课后练习131
阶段进阶练习133
第4教学日135
第1课 设计师职业知识冲压模具分类及
结构136
第2课 模具模架137
4.2.1 模架库137
4.2.2 标准件系统141
课后练习146
第3课 模具冷却系统157
4.3.1 概述158
4.3.2 创建水路图样160
4.3.3 水路参数160
课后练习161
第4课 模具浇注系统165
4.4.1 流道系统165
4.4.2 浇口设计166
课后练习171
第5课 模架附属结构175
4.5.1 滑块和抽芯机构175
4.5.2 电极和镶块设计178
阶段进阶练习181
第5教学日183
第1课 设计师职业知识数控加工基础184
5.1.1 数控加工技术和工艺流程184
5.1.2 NX 10.0加工界面203
第2课 参数组和基本操作206
5.2.1 父参数组操作206
5.2.2 基本操作213
5.2.3 刀具轨迹217
5.2.4 后处理和车间文档219
课后练习220
第3课 面铣削227
5.3.1 平面铣削加工227
5.3.2 面铣削加工252
课后练习258
第4课 型腔铣削264
5.4.1 型腔铣削加工264
5.4.2 插铣削加工272
课后练习278
阶段进阶练习282
第6教学日285
第1课 设计师职业知识数控机床和
系统286
6.1.1 数控机床特点286
6.1.2 数控机床构成287
第2课 轮廓铣削289
6.2.1 深度轮廓铣削加工289
6.2.2 固定轮廓铣削加工295
课后练习307
第3课 点位铣削312
6.3.1 概述312
6.3.2 加工几何314
6.3.3 固定循环321
6.3.4 切削参数325
课后练习326
第4课 车削加工330
6.4.1 概述330
6.4.2 加工几何体332
6.4.3 加工刀具338
6.4.4 粗车操作342
6.4.5 精车操作345
课后练习347
阶段进阶练习353
|
內容試閱:
|
第1教学日
UG NX 10.0提供了塑料注塑模具、铝镁合金压铸模具、钣金冲压模具等模具设计模块,由于塑料注塑模具设计模块涵盖了其他模具设计模块的流程和功能,所以本书主要介绍塑料注塑模具建模的一般流程和加工模块,本书中的所有模具均指注塑模具。
本教学日主要讲解注塑模具设计的一些基础知识、塑料注塑模具建模的一般流程和NX 10.0注塑模向导模块的主要功能,以及使用NX 10.0注塑模向导模块进行模具设计时,如何通过过程自动化、参数全相关技术快速建立模具型芯、型腔、滑块、镶件、模架等模具零件三维实体模型。
第1课 1课时 设计师职业知识模具塑料及成型工艺
1.1.1 模具成型工艺
由于本书所讲解的模具是注塑模具,模具的主要材料为塑料,所以要讲解模具的成型工艺,首先要介绍一下塑料的分类和性能,然后再介绍注塑成型的工作原理和工作参数。
1. 塑料的分类
目前,塑料品种已达300多种,常见的约30多种。可根据塑料的成型性能、使用特点和微观聚集状态对塑料进行分类。
1按成型性能分类
根据成型工艺性能划分,塑料可分为热塑性塑料和热固性塑料。
1热塑性塑料。热塑性塑料的分子链为线性或支链型结构,成型加工时发生物理变化,可反复多次加热软化和冷却硬化。常用的热塑性塑料包括聚氯乙烯、聚乙烯、聚丙烯、聚苯乙烯等。
2热固性塑料。热固性塑料的分子链为体型结构,成型加工时发生化学反应,引起分子间的黏结或交联、硬化或聚合,即使再加热也不能使其恢复到成型前的原始软化状态。常用的热固性塑料包括酚醛塑料、环氧树脂等。
2按塑料的使用特点分类
1通用塑料。通用塑料是指常用的塑料品种,这类塑料产量大、用途广、价格低,包括聚氯乙烯、聚二烯、聚丙烯、聚苯乙烯、酚醛和氨基塑料6种。其产量占整个塑料产量的80%以上。
2工程塑料。工程塑料是指具有优良力学性能的一类塑料,它能代替金属材料,制造承受载荷的工程结构零件。常见的工程塑料包括ABS、聚甲醛、聚碳酸酯、聚酰胺等。
3特种塑料。特种塑料是指具有某一方面特殊性能的塑料如导电、导磁、导热等,用于特殊需求场合。常见的有氟塑料、有机硅等。
3按高分子化合物的微观聚集状态分类
1结晶型塑料。结晶型塑料中,存在树脂大分子的排列呈三相远程有序的区域,即结晶区。一般的结晶型高聚物如尼龙、聚乙烯等,其结晶度为50%~95%。
结晶区的大小对塑料性能有重要影响,一般结晶区越大,分子间作用力越强,塑料的熔点、密度、强度、刚性、硬度越高,耐热性、化学稳定性也越好,但弹性、伸长率、耐冲击性则降低。
2非结晶型塑料。在非结晶型塑料中,组成塑料的大分子链杂乱无章地相互穿插交缠着,无序地堆积在一起。这类塑料的性能主要取决于高聚物本身的特性、分子链的结构、分子量的大小和分子链的长短等因素。常见的非结晶型塑料有ABS、聚碳酸酯、聚苯乙烯等。
2. 塑料的性能
塑料的性能主要指塑料在成型工艺过程中所表现出来的成型特性。在模具的设计过程中,要充分考虑这些因素对塑件的成型过程和成型效果的影响。
1塑料的成型收缩
塑料制件的收缩不仅与塑料本身的热胀冷缩性质有关,而且还与模具结构及成型工艺条件等因素有关,故将塑料制作件的收缩通称为成型收缩。收缩性的大小以收缩率表示,即单位长度塑件收缩量的百分数。
设计模具型腔尺寸时,应按塑件所使用的塑料的收缩率给予补偿,并在塑件成型时调整好模温、注射压力、注射速度及冷却时间等因素以控制零件成型后的最终尺寸。
2塑料的流动性
塑料的流动性是指在成型过程中,塑料熔体在一定的温度和压力作用下填充模腔的能力。
流动性差的塑料,在注塑成型时不易填充模腔,易产生缺料,在塑料熔体的汇合处不能很好地熔接而产生熔接痕。这些缺陷会导致零件报废。反之,若材料的流动性太好,注塑时容易产生溢料飞边和流延现象。浇注系统的形式、尺寸、布置,包括型腔的表面粗糙度、浇道截面厚度、型腔形式、排气系统、冷却系统等模具结构都对塑料的流动性起着重要影响。
热塑性塑料按流动性可分为以下3类。
1流动性好的,有尼龙、聚乙烯、聚苯乙烯、聚丙烯、醋酸纤维等。
2流动性一般的,有ABS、有机玻璃、聚甲醛、聚氯醚。
3流动性差的,有聚碳酸酯、硬聚氯乙烯、聚苯醚、氟塑料。
3塑料的取向和结晶
取向是指由于各向异性导致的塑料在各个方向上收缩不一致的现象。影响取向的因素主要有塑料品种、塑件壁厚、温度等。除此之外,模具的浇口位置、数量、断面大小对塑件的取向方向、取向程度和各个部位的取向分子情况有重大影响,是模具设计中必须重视的问题。
结晶是塑料中树脂大分子的排列呈三相远程有序的现象,影响结晶的主要因素有塑料类型、添加剂、模具温度、冷却速度。结晶率对于塑料的性能有重要的影响,因此在模具设计和塑件成型过程中应予以特别的注意。
4吸湿性
吸湿性是指塑料对水分的亲疏程度。在成型加工过程中,当塑料的水分含量超过一定的限度时,水分在高温料筒中变为气体,促使塑料高温分解,导致成型缺陷。
据此塑料大致可以分为两类:一类是具有吸湿或黏附水分倾向的塑料,例如聚酰胺、聚碳酸酯、ABS、聚苯醚等;另一类是吸湿或黏附水分极少的塑料,如聚乙烯、聚丙烯等。
5热敏性
某些热稳定性差的塑料,在高温下受热时间长、浇口截面过小或剪切作用大时,料温增高就容易发生变色、降解、分解的倾向,塑料的这种特性称为热敏性。为防止热敏性塑料出现过热分解现象,可采取加入稳定剂、合理选样设备、合理控制成型温度和成型周期、及时清理设备等措施。另外,还可以采取给模具表面镀铝、合理设计模具的浇注系统等措施。
3. 注塑成型的工作原理
注塑成型又称注射成型,可以用来生产空间几何形状非常复杂的塑料制品。由于其具有应用广、成型周期短、生产效率高、模具工作条件可以得到改善、制品精度高、生产条件较好、生产操作容易实现自动化和机械化等诸多方面的优点,因此在整个塑料制品生产行业中占有非常重要的地位。
利用塑料的可挤压和可模塑性,首先将松散的粒料或粉状成型物料从注塑机的料斗送入高温的机筒内加热熔解塑化,使之成为黏流态熔体;然后用柱塞或螺杆压缩并推动塑料熔体向前移动,使熔体以很大的流速通过机筒前端的喷嘴,并以很快的速度,注射进入温度较低的闭合模具型腔中;经过一段保压冷却成型时间后,开启模具便可以从模腔中脱出具有一定形状和尺寸的塑料制品。
4. 注塑成型的工艺参数
注塑成型工艺的核心问题,就是采用一切措施以得到塑化良好的塑料熔体,并将塑料熔体注射到型腔中,在控制条件下冷却成型,使塑料达到所要求的质量。注塑成型有三大工艺条件,即温度、压力和成型时间。
1温度
注塑成型过程需控制的温度主要包括模具温度和料温。
1模具温度。模具温度直接影响塑料熔体的充模能力以及塑件的内在性能与外观质量。通常,提高模具温度可以改善熔体的流动性、增强制件的密度和结晶度及减小充模压力。但制件的冷却时间、收缩率和脱模后的翘曲变形将会延长和增大,且生产效率也会因为冷却时间的延长而下降。因此模具冷却系统的设计对于塑件的成型质量和成型效率有着非常重要的影响,是模具设计中需要特别注意的问题。
2料温。料温指塑化物料的温度和从喷嘴注射出的熔体温度。其中,前者称为塑化温度,后者称为注射温度,分别取决于机筒和喷嘴两部分的温度。
料温应根据塑料的熔点和软化点、制作的大小、厚薄、成型时间来确定。通常靠近料斗处较低,喷嘴端较高。
2压力
注塑成型时需要选择与控制的压力包括注射压力、保压力和背压力。其中,注射压力与注射速度相辅相成,对塑料熔体的流动和填充模具有决定性作用。注射压力的大小根据塑料的性能、制件的大小、厚薄和流程长短来确定。在塑料熔体黏度较高、壁薄、流程长等情况下,适合采用较高的注射压力。
3成型时间
成型时间是指完成依次注射成型全过程所需要的时间。成型时间过长,在料筒中原料会因受热时间过长而分解,制件会因应力大而降低机械强度。成型时间过短,会因塑化不完全导致制件易变形。因此,合理的成型时间是保证制件质量、提高生产率的重要条件。
1.1.2 模具的结构和类别
下面介绍注塑模具的结构和类别。
1. 注塑模具的典型结构
注塑模具由动模和定模两部分组成,动模安装在注射机的移动模板上,定模安装在注射机的固定模板上。成型时,动模与定模闭合构成浇注系统和型腔,开模时动模与定模分离,以便取出塑料制品。根据各部件的作用,注塑模具可分为以下几个基本组成部分。
1浇注系统
浇注系统又称流道系统,其作用是为塑料熔体提供从注射机喷嘴流向型腔的通道,包括主流道、分流道、浇口、冷料穴、钩料杆等。
2成型部件
成型部件主要是由型腔和型芯组成。型芯形成制品的内表面形状,型腔形成制品的外表面形状。
3导向部件
导向部件的主要作用是保证各结构组件相互之间的移动精度。导向部件通常由导柱、导套或导滑槽组成。
4推出机构
推出机构或称顶出机构,主要作用是将塑件从模具中脱出,以及将凝料从流道内拉出并卸除。推出机构通常由推杆或推管、推环、推块、推板、推杆固定板、推板、拉料杆、流道推板组成。
5温控系统
为了满足注射工艺对模具温度的要求,需要调温系统对模具的温度进行调节,对模具进行加热或冷却。热塑性塑料的模具温控系统主要是对模具进行冷却。常用的方法是在模具内开设冷却水道,利用循环冷却水带走模具冷却时需要散除的热量。对于热固性塑料,采用注塑模具或热流道模具通常需要加热,可以采取通蒸汽的方法提高或保持模具温度,有时也需要在模具内部和周围安装电加热元件,因此需要在模具内设置加热孔或安装加热板以及防止热量散失的隔热板。
6排气槽
排气槽的作用是将成型过程中的气体充分排除,防止塑件产生气穴等缺陷,常用的办法是在分型面处或容易困气的部位开设排气沟槽。分型面、镶块、推杆之间存在微小的间隙,若它们可以达到排除气体的目的,可不必开设排气槽。
7侧抽芯机构
对于带有侧凹、侧凸或侧孔的塑件,若将成型部件做成整体,则成型完成后塑件将无法脱模。因此需要在模具中设置侧抽芯机构,以便在塑件成型后,该机构能在塑件脱模之前先行让出,保证塑件顺利脱模。
8模架
模架的主要作用是将各结构件组成整体的连接系统,包括定模座板、定模板、动模板、动模座板等。通常采用标准件,以减少繁重的模具设计与制造工作量。
2. 塑料模具的一般类别
塑料模具的一般类别可以按照模具的板模层数来划分,大致可分为下面几种。
1两板模
两板模2 PLATE MOLD又称单一分型面模,它是注塑模中最简单的一种。但是,其他模具都是两板模的发展,可以说,两板模是其他模具的基础。
两板模以分型面为界将整个模具分为两部分:动模和定模。
两板模的一部分型腔在动模,一部分型腔在定模;主流道在定模部分,分流道开设在分型面上。开模后,制品和流道留在定模,定模部分设有顶出系统以便取出制品,其常用结构如图1-1所示。
2三板模或细水口模
三板模或细水口模3 PLATE MOLD, PIN-POINT GATE MOLD是由两个分型面将模具分成三部分的塑料模具,它的结构比两板模复杂,设计和加工的难度也比较高。三板模比两板模增加了浇口板,适用于制品的四周不准有浇口痕迹的场合,这种模具采用点浇口,所以叫细水口模具。这种模具的结构比较复杂,启动动力一般使用山打螺丝或拉板机构,如图1-2所示。
图1-1 两板模具的结构 图1-2 三板模具的结构
3热流道模
热流道模HOT RUNNER MANIFOLD是一种新兴的模具类型,它的制作成本相比前两种模具结构都要高,制作复杂,不易加工。但是热流道模有很多无法比拟的优点,例如热流道模借助加热装置使浇注系统中的塑料不会凝固,也不会随制品脱模,更节省材料和周期,所以热流道模又称无流道模。
一般认为,热流道模具具有如下优点:①无废料产生;②可降低注射压力,可以采用多腔模;③可大幅缩短成型周期;④可大幅提高制品的品质。
但是,并不是所有的塑料都适合使用热流道模具进行加工,适合热流道模的塑料一般具有如下特点:①塑料的熔融温度范围较宽,在处于低温状态时,流动性好;高温状态时,具有较好的热稳定性。②用于热流道模具的塑料对压力相对敏感,不加压力不流动,但施加压力时即可流动。③比热小,易熔融,而且又易冷却。④导热性好,便于在模具中很快冷却。
目前,用于热流道模具的塑料有ABS、PC、PE、POM、HIPS、PS等。我们现在常用的热流道有两种: 加热流道模具见图1-3,绝热流道模具见图1-4。
图1-3 加热流道模具 图1-4 绝热流道模具
第2课 2课时 模具设计基础知识
下面介绍模具设计的基本流程,以及模具型腔设计的一些基本概念和方法。
1.2.1 模具设计的基本流程
由于注塑模具的多样性和复杂性,很难总结可以普遍适用于实际情况的注塑模具的设计步骤,这里所列出的设计步骤仅为基本流程,实际的流程可能还会有很大变化。
1选择成型设备。
2拟定模具结构方案。
拟定模具结构方案的主要内容如下。
①分析塑件注塑工艺性。
②确定成型方案与模具的总体结构。
③选择模具零件材料。
④设计成型零件。
⑤确定型腔数目。
⑥确定型腔布局与尺寸。
⑦选择分型面。
⑧创建浇口和流道。
⑨设计冷却系统。
⑩设计机械运动机构。
?设计顶出及导向定位机构。
?考虑排气系统设计。
?模具总装等。
3绘制模具装配草图。
4绘制装配图。
5绘制零件图。
1.2.2 模具型腔的设计
下面介绍设计模具型腔的基本方法。
1. 注塑模成形零部件的结构
成形塑料件外表面的零件称为凹模或型腔,型芯是成形塑料件的内表面,成形杆可以用作成形制品的局部细节。成形零部件是在一定温度和压力下使用的零件,故对其尺寸、强度和刚度、材料和热处理工艺、机械加工都有相应的要求。
2. 型腔的结构设计
型腔按结构形式可分为整体式、整体嵌入式、局部镶嵌式和组合式四种。
1整体式型腔
整体式型腔是把型腔加工在一个整块零件上,如图1-5所示。整体式型腔具有强度高、刚度好的优点,但对于形状复杂的塑料件,其加工困难,热处理不方便,因而适用于形状比较简单的塑料件。
随着加工方法不断的改进,整体式型腔的适用范围已越来越广。
2整体嵌入式型腔
整体嵌入式型腔仍然是把型腔加工在一个整块零件上,但会在该零件中嵌入另一个零件,主要适用于塑料件生产批量较大时采用一模多腔的模具。为了保证各型腔的尺寸和表面状况一致,或为减少切削工作量,有时也是为了型腔部分采用优质钢材,整体嵌入式型腔采用冷挤压或其他方法,如图1-6所示。
图1-6 整体嵌入式型腔
3局部镶嵌式型腔
型腔的某一部分形状特殊,或易损坏需要更换时,可以采用整体型腔,但特殊形状部分采用局部镶嵌方法。如图1-7所示,型腔侧表面有突出肋条,可以将此肋条单独加工,然后采用T形槽、燕尾槽或圆形槽镶入型腔内;图1-8所示型腔底部中间带有波纹,可将该部分单独加工为独立零件,再镶入型腔底部构成完整型腔。
图1-7 局部镶嵌式型腔 图1-8 型腔底部中间带有波纹
4组合式型腔
组合式型腔的侧壁和底部由不同零件组合而成,多用于生产尺寸较大的塑料件,为了型腔加工、热处理、抛光研磨的方便,可以将完整的型腔分为几个部分,分别加工后再组合为一体。根据塑料件结构的特点,组合式型腔大致有整体侧壁与腔底组合、四壁组合后再与底部组合两种不同形式。
图1-9所示是将侧壁用螺钉连接,无配合部分,结构简单,加工迅速,但在成形过程中连接面容易楔入塑料,且加工侧壁时应防止侧面下端的棱边损伤。
图1-10所示是底部与侧壁拼合时增加了一个配合面,螺钉穿过配合面进行连接。配合面采用过渡配合,可防止塑料揳入连接面。
图1-9 侧壁用螺钉连接的组合式型腔 图1-10 增加了配合面的组合式型腔
图1-11所示的结构形式在型腔组成上与图1-10相同,但不是用螺钉直接将型腔底部与侧壁连接,而是增加了一块垫板,靠垫板将两者压紧,再将垫板与侧壁用螺钉紧固连接。
图1-12所示是四壁相拼合套入模套中,再与腔底拼合,下面垫上垫板,用螺钉与模套连接。四壁拼合采用互相扣锁形式,为保证扣锁的紧密性,四处边角扣锁的接触面应留有一段非接触部分,留出0.3~0.4mm的间隙。基于同样原因,四壁转角处的圆角半径R应大于模套转角处的半径r。
图1-11 增加了垫板的组合式型腔 图1-12 侧壁组合后再与底部组合的型腔
图1-13所示的是四壁互相扣锁拼合后与腔底扣锁并连接的形式。
设计镶嵌式和组合式型腔时,应尽可能满足下列要求。
1将型腔的内部形状变为镶件或组合件的外形加工。
2拼缝应避开型腔的转角或圆弧部分,并与脱模方向一致。
3镶嵌件和组合件的数量要力求少,以减少对塑料件外观和尺寸精度的影响。
4易损部分应设计为独立的镶拼件,便于更换。
5组合件的结合面应采用凹凸槽互相扣锁,防止在压力作用下产生位移。
3.型芯和成形杆的设计
成形塑料件内表面的零件统称凸模或称为型芯。对于结构简单的容器、壳、罩、盖、帽、套等塑料件,成形其主体部分内表面的型芯称为主型芯或凸模,而将成形其他小孔或细微结构的型芯称为小型芯或成形杆。型芯按复杂程度和结构形式大致分为以下几种类型。
1整体式型芯
这是形状最简单的主型芯,用一整块材料加工而成,结构牢固,加工方便,但仅适用于塑料件内表面形状简单的情况,如图1-14所示。
2嵌入式型芯
嵌入式型芯的外形比较简单,主要有圆形、方形等。最常采用的嵌入形式是型芯带有凸肩,型芯嵌入固定板的同时,凸肩部分沉入固定板的沉孔部分,再垫上垫板,并用螺钉将垫板与固定板连接,如图1-15所示。另一种嵌入方法是在固定板上加工出盲沉孔,型芯嵌入盲沉孔后用螺钉直接与固定板连接,如图1-16所示。
图1-14 整体式型芯 图1-15 带有凸肩的型芯图1-16 嵌入盲沉孔的型芯
3异形型芯结构形式
对于形状特殊或结构复杂的型芯,需要采用组合式结构或特殊固定形式,但应视具体形状而定,下面以具体实例说明。
图1-17中,型芯成形部分断面是矩形,但为了便于在固定板中固定,固定部分设计为圆形。
图1-18中,型芯比较复杂,可以分别设计为两个零件,组合后再固定到模板中。
图1-17 成形部分断面是矩形的型芯 图1-18 成形部分是五角形的型芯
4小型芯安装固定形式
直径较小的型芯,如果数量较多,采用凸肩垫板安装方法比较好。若各型芯之间距离较近,可以在固定板上加工出一个大的公用沉孔如图1-19所示,因为对每个型芯分别加工出单独的沉孔,孔间壁厚较薄,热处理时易出现裂纹。各型芯的凸肩如果重叠干涉,可将相干涉的一面削掉一部分。
对于单个小型芯,既可以采用凸肩垫板的固定方法,也可采用省去垫板的固定方法。
图1-20是凸肩垫板的固定方法。
图1-19 加工出公用沉孔的型芯 图1-20 凸肩垫板的固定方法
图1-21中,为使安装方便,可将型芯固定部分仅留3~5mm的长度,以防止塑料进入,其余部分可扩大0.5~1mm。
图1-22所示型芯的修磨与更换方便,打开垫板更换型芯下部的支撑销,即可调节型芯的安装高度。
图1-21 固定部分仅留3~5mm 图1-22 修磨与更换方便的型芯
图1-23和图1-24都是省去垫板的固定方法。图1-23采用过渡配合或小间隙配合,另一端铆死;图1-24中的型芯仍带凸肩,用螺丝将凸肩拧紧。
图1-23 过渡配合或小间隙配合的固定 图1-24 带凸肩的固定
第3课 2课时 UG NX 10.0模具模块
NX注塑模向导是一个非常好用的工具,它使模具设计中耗时、烦琐的操作变得更精确、便捷,使模具设计完成后的产品能自动更新相应的模具零件,大大地提高了模具设计师的工作效率。在介绍NX注塑模向导之前,首先来了解一下NX模具设计的术语。
1.3.1 NX模具设计术语
NX的模具设计过程使用了很多术语描述设计步骤,这些是模具设计所独有的,熟练掌握这些术语,对理解NX模具设计有很大的帮助,下面将分别说明。
1设计模型:模具设计必须有一个设计模型,也就是模具将要制造的产品原型。设计模型决定了模具型腔的形状,成型过程是否要利用砂芯、销、镶块等模具元件,以及浇注系统、冷却水线系统的布置。
2参照模型:设计模型在模具模型中的映像。如果在零件设计模块中编辑更改了设计模型,那么包含在模具模型中的参照模型也将发生相应的变化;但是若在模具模型中对参照模型进行编辑,修改其特征,则不会影响设计模型。
3工件:表示直接参与熔料如顶部和底部嵌入物成型的模具元件的总体积。使用分型面分割工件,可以得到型腔、型芯等元件。工件的体积应当包围所有参考模型、模穴、浇口、流道和模口等。
4分型面:分型面由一个或多个曲面特征组成,如图1-26所示,可以分割工件或者已存在的模具体积块。分型面在NX模具设计中占据着重要和最为关键的地位,应当合理地选择分型面的位置。
5收缩率:注塑件从模具中取出冷却至室温后尺寸缩小变化的特性称为收缩性,衡量塑件收缩程度大小的参数称为收缩率。对高精度塑件,必须考虑收缩给塑件尺寸形状带来的误差。
6拔模斜度:塑料冷却后会产生收缩,使塑料制件紧紧地包住模具型芯或型腔突出部分,造成脱模困难。为了便于塑料制件从模具中取出或是从塑料制件中抽出型芯,防止塑料制件与模具成型表面黏附,从而防止塑件制件表面被划伤、擦毛等问题的产生,塑料制件的内、外表面沿脱模方向都应该有倾斜的角度,即脱模斜度,又称为拔模斜度。
图1-26 分型面
1.3.2 注塑模设计界面介绍
打开UG NX 10.0后,选择【文件】|【所有应用模块】|【注塑模向导】命令,进入注塑模向导应用模块,如图1-28所示。
图1-28 选择【注塑模向导】命令
此时将打开【注塑模向导】选项卡,如图1-29所示。使用UG NX 10.0注塑模向导提供的实体工具和片体工具,可以快速、准确地对分模体进行实体修补、片体修补、实体分割等操作。鼠标指针放到选项卡工具条中的按钮上会显示按钮的名称,常用按钮的功能简述如下。
图1-29 【注塑模向导】选项卡
1【初始化项目】按钮:用来载入需要进行模具设计的产品零件。载入零件后,系统将生成用于存放布局、型腔、型芯等的一系列文件。所有用于模具设计的产品三维实体模型都是通过单击该按钮进行产品装载的,设计师要在一副模具中放置多个产品需要多次单击该按钮。
2【多腔模设计】按钮:在一个模具里可以生成多个塑料制品的型芯和型腔。单击该按钮,选择模具设计当前产品模型,只有被选作当前产品才能对其进行模坯设计和分模等操作;需要删除已装载产品时,也可单击该按钮进入产品删除界面。
3【模具CSYS】按钮又称坐标系统:该功能用来设置模具坐标系统。模具坐标系统主要用来设定分模面和拔模方向,并提供默认定位功能。在UG NX 10.0的注塑模向导系统中,坐标系统的XC-YC平面定义在模具动模和定模的接触面上,模具坐标系统的ZC轴正方向指向塑料熔体注入模具主流道的方向。模具坐标系统设计是模具设计中相当重要的一步,模具坐标系统与产品模型的相对位置决定了产品模型在模具中的放置位置和模具结构,是模具设计成败的关键。
4【收缩】按钮:单击该按钮设定产品收缩率可以补偿金属模具模腔与塑料熔体的热胀冷缩差异。UG NX 10.0注塑模向导按设定的收缩率对产品三维实体模型进行放大并生成一个名为shrink part的三维实体模型,后续的分型线选择、补破孔、提取区域、分型面设计等分模操作均以此模型为基础进行操作。
5【工件】按钮又称作模具模坯:单击该按钮设计模具模坯,UG NX 10.0注塑模向导自动识别产品外形尺寸并预定义模坯的外形尺寸,其默认值在模具坐标系统六个方向上比产品外形尺寸大25mm。
6【型腔布局】按钮:单击该按钮设计模具型腔布局,注塑模向导模具坐标系统定义的是产品三维实体模型在模具中的位置,但它不能确定型腔在XC-YC平面中的分布。注塑模向导模块提供该按钮设计模具型腔布局,系统提供了矩形排列和圆形排列两种模具型腔排布方式。
7【模架库】按钮:模架是用来安放和固定模具的安装架,并把模具系统固定在注塑机上。单击该按钮可以调用UG NX 10.0注塑模向导提供的电子表格驱动标准模架库,模具设计师也可在此定制非标模架。
8【标准件库】按钮:单击该按钮可以调用UG NX 10.0注塑模向导提供的定位环、主流道衬套、导柱导套、顶杆、复位杆等模具标准件。
9【顶杆后处理】按钮:单击该按钮可以利用分型面和分模体提取区域对模具推杆进行修剪,使模具推杆长度尺寸和头部形状均符合要求。
10【滑块和浮生销库】按钮:单击该按钮可以调用UG NX 10.0注塑模向导提供的滑块体、内抽芯三维实体模型。
11【子镶块库】按钮:单击该按钮可以对模具子镶块进行设计。子镶块的设计是对模具型腔、型芯的进一步细化设计。
12【浇口库】按钮:单击该按钮可以对模具浇口的大小、位置、浇口形式进行设计。
13【流道】按钮:单击该按钮可以对模具流道的大小、位置、排布形式进行设计。
14【冷却标准件库】按钮:单击该按钮可以对模具冷却水道的大小、位置、排布形式进行设计,同时可按设计师的设计意图在此选用模具冷却水系统使用的密封圈、堵头等模具标件。
15【电极】按钮:单击该按钮可以对模具型腔或型芯上形状复杂、难于加工的区域设计加工电极。UG NX 10.0注塑模向导提供了两种电极设计方式,即标准件方式和包裹体方式。
16【修边模具组件】按钮:单击该按钮利可以利用模具零件三维实体模型或分型面、提取区域对模具进行修剪,使模具标件的长度尺寸和形状均符合要求。
17【腔体】按钮:单击该按钮可以对模具三维实体零件进行建腔操作。建腔即是利用模具标准件、镶块外形对目标零件型腔、型芯、模板进行挖孔、打洞,为模具标准件、镶块安装制造空间。
18【物料清单】按钮:单击该按钮可以对模具零部件进行统计汇总,生成模具零部件汇总的物料清单。
19【装配图纸】按钮:单击该按钮可以进行模具零部件二维平面出图操作。
1.3.3 NX塑料注塑模具的设计流程
NX塑料注塑模具的设计过程遵循模具设计的一般规律,主要的流程如下。
1. 产品模型准备
用于模具设计的产品三维模型文件有多种文件格式,UG NX 10.0注塑模向导模块需要一个NX 文件格式的三维产品实体模型作为模具设计的原始模型。如果模型不是NX 文件格式的三维实体模型,则需用NX 软件将文件转换成NX 文件格式的三维实体模型或是重新创建NX三维实体模型。正确的三维实体模型有利于UG NX 10.0注塑模向导模块自动进行模具设计。
2. 产品加载和初始化
产品加载是使用UG NX 10.0注塑模向导模块进行模具设计的第一步,产品成功加载后,NX注塑模向导模块将自动产生一个模具装配结构,该装配结构包括构成模具所必需的标准元素。
3. 设置模具坐标系统
设置模具坐标系统是模具设计中相当重要的一步,模具坐标系统的原点须设置于模具动模和定模的接触面上,模具坐标系统的XC-YC平面须定义在动模和定模的接触面上,模具坐标系统中ZC轴的正方向指向塑料熔体注入模具主流道的方向。模具坐标系统与产品模型的相对位置决定产品模型在模具中的放置位置,是模具设计成败的关键。
4. 计算产品收缩率
塑料熔体在模具内冷却成型为产品后,由于塑料的热胀冷缩大于金属模具的热胀冷缩,所以成型后的产品尺寸将略小于模具型腔的相应尺寸,因此模具设计时模腔的尺寸要求略大于产品的相应尺寸以补偿金属模具型腔与塑料熔体的热胀冷缩差异。UG NX 10.0模具向导处理这种差异的方法是将产品模型按要求放大生成一个名为缩放体的分模实体模型,该实体模型的参数与产品模型参数是全相关的。
5. 设定模具型腔和型芯毛坯尺寸
模具型腔和型芯毛坯简称模坯是外形尺寸大于产品尺寸,用于加工模具型腔和型芯的金属坯料。UG NX 10.0注塑模向导模块自动识别产品的外形尺寸,并预定义模具型腔、型芯毛坯的外形尺寸,其默认值在模具坐标系六个方向上比产品外形尺寸大25mm。NX模具向导通过分模将模具坯料分割成模具型腔和型芯。
6. 模具型腔布局
模具型腔布局即是通常所说的一模几腔,指的是产品模型在模具型腔内的排布数量。UG NX 10.0注塑模向导模块提供了矩形排列和圆形排列两种模具型腔排布方式。
7. 建立模具分型线
UG NX 10.0注塑模向导模块提供了MPVMould Part Validation,分模对象验证功能,可以将分模实体模型表面分割成型腔区域和型芯区域两种面,两种面相交产生的一组封闭曲线就是分型线。
8. 修补分模实体模型破孔
塑料产品由于功能或结构需要,在产品上常有一些穿透产品孔,即所称的破孔。为将模坯分割成完全分离的两部分型腔和型芯,UG NX 10.0注塑模向导模块需要用一组厚度为零的片体将分模实体模型上的这些孔封闭起来,这些厚度为零的片体和分型面、分模实体模型表面可将模坯分割成型腔和型芯。NX注塑模向导模块提供了自动补孔功能。
9. 建立模具分型面
分型面是由分型线向模坯四周按一定方式扫描、延伸、扩展而形成的一组连续封闭曲面。UG NX 10.0注塑模向导模块提供了自动生成分型面功能。
10. 建立模具型腔和型芯
分模实体模型破孔修补和分型面创建后,即可用UG NX 10.0注塑模向导模块提供的建立模具型腔和型芯功能,将模坯分割成型腔和型芯。
11. 使用模架
模具型腔、型芯建立后,需要提供模架以固定模具型腔和型芯。UG NX 10.0注塑模向导模块提供有电子表格驱动的模架库和模具标件库。
12. 加入模具标准件
模具标件是指模具定位环、主流道衬套、顶杆、复位杆等模具配件。UG NX 10.0注塑模向导模块提供有电子表格驱动的三维实体模具标件库。
13. 模具建腔
建腔是指在模具型腔、型芯、模板上建立腔、孔等特征以安装模具型腔、型芯、镶块及各种模具标件。
课后练习
ywj\01\01.prt
光盘\视频课堂\第1教学日\1.3
练习案例的分析如下。
本课课后练习创建塑料瓶盖。不同的瓶盖有不同的用途,如无菌冷灌装盖、热灌装盖、常温无内压水盖和汽盖。瓶盖从结构上又分内塞型和垫片型。图1-31所示是完成的塑料瓶盖模型。
本课案例主要练习NX 10的模型创建知识,其中草图是进行三维特征生成前需要了解的基础知识。在UG中,草图的绘制原则和常见的CAD软件类似,可以快速上手。学好本案例内容能更容易地掌握NX 10的草图绘制和模型创建基本知识。创建塑料瓶盖模型的思路和步骤如图1-32所示。
图1-31 塑料瓶盖模型 图1-32 创建塑料瓶盖模型的步骤
练习案例的具体操作步骤如下。
创建瓶盖的主体。选择【文件】|【新建】命令,弹出【新建】对话框,设置文件名称,如图1-33所示,单击【确定】按钮。
图1-33 新建模型
在【直接草图】工具条中单击【草图】按钮,弹出【创建草图】对话框,选择草绘平面,如图1-34所示,单击【确定】按钮。
图1-34 【创建草图】对话框
在【直接草图】工具条中,单击【圆】按钮,绘制直径为20的圆本书数字单位按机械惯例统一为毫米,不再专门标出,如图1-35所示。
在【特征】工具条中,单击【拉伸】按钮,弹出【拉伸】对话框,选择圆形草图,设置【距离】参数为15,如图1-36所示,单击【确定】按钮,创建拉伸特征。
在【特征】工具条中,单击【边倒圆】按钮,弹出【边倒圆】对话框,创建半径为2的圆角,如图1-37所示,单击【确定】按钮,创建圆角。
在【特征】工具条中,单击【抽壳】按钮,弹出【抽壳】对话框,选择去除面,设置【厚度】为0.8,如图1-38所示,单击【确定】按钮,创建抽壳特征。
图1-35 绘制直径为20的圆形 图1-36 拉伸圆形
图1-37 创建圆角 图1-38 创建抽壳特征
创建阵列特征,在【特征】工具条中,单击【基准平面】按钮,弹出【基准平面】对话框,创建【距离】为13的基准平面,单击【确定】按钮,如图1-39所示。
在【直接草图】工具条中单击【草图】按钮,弹出【创建草图】对话框,选择草绘平面,如图1-40所示,单击【确定】按钮。
在【直接草图】工具条中,单击【圆】按钮,绘制直径为20的圆,如图1-41所示。
在【直接草图】工具条中,单击【矩形】按钮,弹出【矩形】对话框,绘制0.40.4的矩形,如图1-42所示。
在【直接草图】工具条中,单击【三点圆弧】按钮,绘制半圆弧,如图1-43所示。
在【直接草图】工具条中,单击【快速修剪】按钮,修剪草图,如图1-44所示。
在【特征】工具条中,单击【拉伸】按钮,弹出【拉伸】对话框,选择草图,设置【距离】参数为9,如图1-45所示,单击【确定】按钮,创建拉伸特征。
在【特征】工具条中,单击【阵列特征】按钮,弹出【阵列特征】对话框,设置圆形阵列【数量】为72,如图1-46所示,单击【确定】按钮,创建阵列特征。
在【直接草图】工具条中单击【草图】按钮,弹出【创建草图】对话框,选择草绘平面,如图1-47所示,单击【确定】按钮。
图1-39 创建基准面 图1-40 【创建草图】对话框
图1-41 绘制直径为20的圆形图1-42 绘制0.40.4的矩形图1-43 绘制半圆弧
图1-44 修剪草图 图1-45 创建拉伸特征
图1-46 创建阵列特征 图1-47 【创建草图】对话框
在【直接草图】工具条中,单击【矩形】按钮,弹出【矩形】对话框,绘制140.5的矩形,如图1-48所示。
在【特征】工具条中,单击【拉伸】按钮,弹出【拉伸】对话框,选择草图,修改【距离】参数为15,如图1-49所示,单击【确定】按钮,创建拉伸切除特征。
图1-48 绘制140.5的矩形 图1-49 创建拉伸切除特征
在【特征】工具条中,单击【阵列特征】按钮,弹出【阵列特征】对话框,设置圆形阵列【数量】为4,如图1-50所示,单击【确定】按钮,创建圆形阵列。
在【直接草图】工具条中单击【草图】按钮,弹出【创建草图】对话框,选择草绘平面,如图1-51所示,单击【确定】按钮。
图1-50 创建圆形阵列 图1-51 【创建草图】对话框
在【直接草图】工具条中,单击【圆】按钮,绘制直径为20的圆,如图1-52所示。
在【直接草图】工具条中,单击【矩形】按钮,弹出【矩形】对话框,绘制2.80.2的矩形,如图1-53所示。
图1-52 绘制直径为20的圆形 图1-53 绘制2.80.2的矩形
在【直接草图】工具条中,单击【快速修剪】按钮,修剪草图,如图1-54所示。
在【特征】工具条中,单击【拉伸】按钮,弹出【拉伸】对话框,选择草图,设置【距离】参数为2,如图1-55所示,单击【确定】按钮,创建拉伸特征。
在【特征】工具条中单击【拔模】按钮,打开【拔模】对话框,选择拔模面,设置拔模【角度】为30,如图1-56所示,单击【确定】按钮,创建拔模特征。
在【特征】工具条中,单击【阵列特征】按钮,弹出【阵列特征】对话框,设置圆形阵列【数量】为16,如图1-57所示,单击【确定】按钮,创建圆形阵列。
创建螺纹。在【直接草图】工具条中单击【草图】按钮,弹出【创建草图】对话框,选择草绘平面,如图1-58所示,单击【确定】按钮。
在【直接草图】工具条中单击【圆】按钮,绘制直径为13和14的同心圆,如图1-59所示。
在【特征】工具条中,单击【拉伸】按钮,弹出【拉伸】对话框,选择草图,设置【距离】参数为2,如图1-60所示,单击【确定】按钮,创建拉伸特征。
在【直接草图】工具条中单击【草图】按钮,弹出【创建草图】对话框,选择草绘平面,如图1-61所示,单击【确定】按钮。
图1-54 修剪草图 图1-55 创建拉伸特征
图1-56 创建拔模特征图1-57 创建圆形阵列
图1-58 【创建草图】对话框图1-59 绘制同心圆
图1-60 创建拉伸特征图1-61 【创建草图】对话框
在【直接草图】工具条中,单击【直线】按钮,绘制梯形,尺寸如图1-62所示。
图1-62 绘制梯形
在【曲线】工具条中,单击【螺旋线】按钮,弹出【螺旋线】对话框,设置参数如图1-63所示,创建螺旋线。
在【曲面】工具条中,单击【扫掠】按钮,弹出【扫掠】对话框,选择截面和引导线,如图1-64所示,单击【确定】按钮,创建扫掠特征。
图1-63 创建螺旋线 图1-64 创建扫掠特征
在【特征】工具条中,单击【合并】按钮,弹出【合并】对话框,选择目标和工具,如图1-65所示,单击【确定】按钮,创建合并特征。
完成的瓶盖模型如图1-66所示。
图1-65 创建合并特征 图1-66 完成的瓶盖模型
|
|